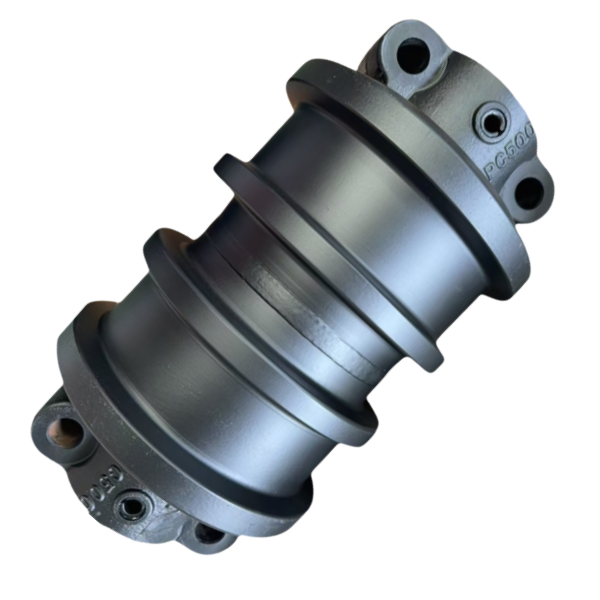
KOMATSU/PC500/SF/DF/208-30-00462/track-roller supply
Product Specifications
KOMATSU excavator/PC500/SF/DF/208-30-00462/track-roller
Excavator Track Roller: Comprehensive Guide
1. Definition & Function
Primary Role: Supports the excavator's weight and guides the track chain along the undercarriage.
Key Functions:
Distributes machine load evenly across tracks
Maintains track alignment (prevents lateral slippage)
Reduces friction between track links and undercarriage
Primary Role: Supports the excavator's weight and guides the track chain along the undercarriage.
Key Functions:
Distributes machine load evenly across tracks
Maintains track alignment (prevents lateral slippage)
Reduces friction between track links and undercarriage
2. Types of Track Rollers
Type Design Features Applications Single-Flange One raised edge on outer side Standard excavators, flat terrain Double-Flange Flanges on both sides Rough terrain, slope operations Sealed/Lubricated Grease-filled with dust seals High-hour machines, abrasive environments Non-Flanged Smooth cylindrical surface Specialized low-speed applications
Type | Design Features | Applications |
---|---|---|
Single-Flange | One raised edge on outer side | Standard excavators, flat terrain |
Double-Flange | Flanges on both sides | Rough terrain, slope operations |
Sealed/Lubricated | Grease-filled with dust seals | High-hour machines, abrasive environments |
Non-Flanged | Smooth cylindrical surface | Specialized low-speed applications |
3. Critical Specifications
Bore Size: Matches pin diameter (common: 40-100mm)
Roller Width: Varies by machine class (mini excavator vs. 50-ton+)
Material:
Shell: Hardened alloy steel (HRC 55+)
Bushings: Bronze or composite alloys
Load Rating: Typically 5-30 tons per roller
Bore Size: Matches pin diameter (common: 40-100mm)
Roller Width: Varies by machine class (mini excavator vs. 50-ton+)
Material:
Shell: Hardened alloy steel (HRC 55+)
Bushings: Bronze or composite alloys
Load Rating: Typically 5-30 tons per roller
4. Wear Indicators
Visual Signs:
3mm flange wear
Flat spots >10% of roller circumference
Visible cracks or spalling
Operational Symptoms:
Track misalignment
Unusual grinding noises
Increased track slap/vibration
Visual Signs:
3mm flange wear
Flat spots >10% of roller circumference
Visible cracks or spalling
Operational Symptoms:
Track misalignment
Unusual grinding noises
Increased track slap/vibration
5. Maintenance Best Practices
Inspection Frequency:
Every 250 operating hours (severe duty)
Every 500 hours (normal conditions)
Lubrication:
Grease type: NLGI #2 lithium complex
Interval: Per OEM manual (typically 8-50 hours)
Replacement Protocol:
Always replace in matched sets
Verify track chain wear compatibility
Torque bolts to manufacturer specs
Inspection Frequency:
Every 250 operating hours (severe duty)
Every 500 hours (normal conditions)
Lubrication:
Grease type: NLGI #2 lithium complex
Interval: Per OEM manual (typically 8-50 hours)
Replacement Protocol:
Always replace in matched sets
Verify track chain wear compatibility
Torque bolts to manufacturer specs
6. OEM vs Aftermarket Considerations
OEM Advantages:
Precise metallurgical specifications
Warranty coverage
Guaranteed fitment
Aftermarket Value:
Cost savings (30-50% less)
Improved designs (e.g., triple-lip seals)
Faster availability for older models
OEM Advantages:
Precise metallurgical specifications
Warranty coverage
Guaranteed fitment
Aftermarket Value:
Cost savings (30-50% less)
Improved designs (e.g., triple-lip seals)
Faster availability for older models
7. Failure Analysis
Failure Mode Root Cause Preventive Action Seal leakage Contaminated grease Regular undercarriage cleaning Bushing wear Improper lubrication Use high-temp extreme pressure grease Flange fracture Track tension too high Follow OEM tension specs Axle seizure Water intrusion Submerge testing during rebuilds
Failure Mode | Root Cause | Preventive Action |
---|---|---|
Seal leakage | Contaminated grease | Regular undercarriage cleaning |
Bushing wear | Improper lubrication | Use high-temp extreme pressure grease |
Flange fracture | Track tension too high | Follow OEM tension specs |
Axle seizure | Water intrusion | Submerge testing during rebuilds |
8. Global Market Overview
Top Manufacturers:
Japan: Komatsu, Hitachi
Europe: Berco, Liebherr
USA: Caterpillar, ITR
Korea: Doosan, Hyundai
Price Range:
Mini excavator: 200/roller
20-ton class: 600/roller
Mining excavators: $1,500+/roller
Top Manufacturers:
Japan: Komatsu, Hitachi
Europe: Berco, Liebherr
USA: Caterpillar, ITR
Korea: Doosan, Hyundai
Price Range:
Mini excavator: 200/roller
20-ton class: 600/roller
Mining excavators: $1,500+/roller
9. Installation Tips
Clean mounting surfaces thoroughly
Pre-lubricate bushings before assembly
Use proper hoisting equipment (rollers weigh 15-150kg)
Stage replacements during undercarriage overhauls
Clean mounting surfaces thoroughly
Pre-lubricate bushings before assembly
Use proper hoisting equipment (rollers weigh 15-150kg)
Stage replacements during undercarriage overhauls
10. Emerging Technologies
Smart Rollers: Embedded sensors for wear monitoring
Composite Materials: Polymer-coated rollers for wet environments
Modular Designs: Quick-change cartridge systems
Smart Rollers: Embedded sensors for wear monitoring
Composite Materials: Polymer-coated rollers for wet environments
Modular Designs: Quick-change cartridge systems
This technical breakdown covers all critical aspects of track rollers while maintaining clear organization for easy reference. The table-based comparisons and structured sections enable quick comprehension of complex engineering considerations. Would you like additional details on any specific section?